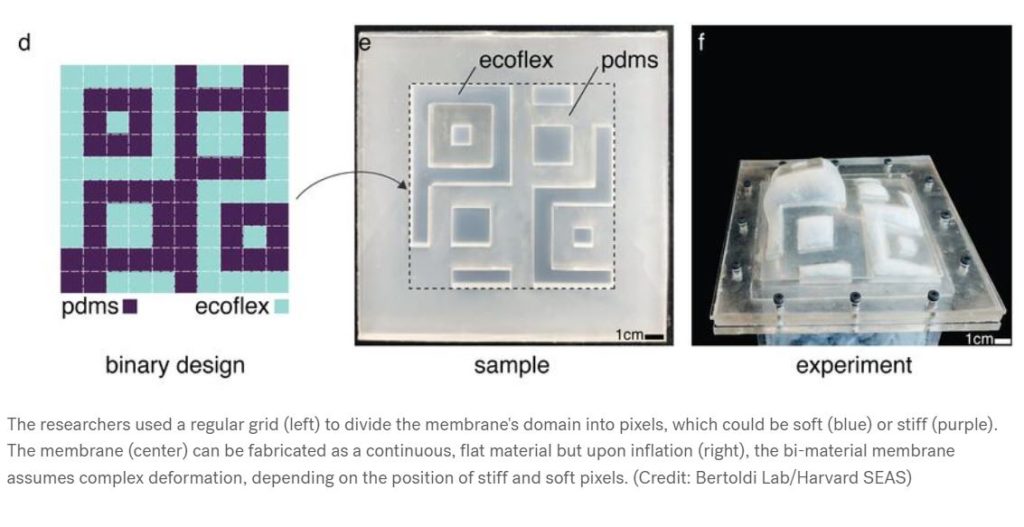
New platform can program the transformation of 2D stretchable surfaces into specific 3D shapes. Flat materials that can morph into three-dimensional shapes have potential applications in architecture, medicine, robotics, space travel, and much more. But programming these shape changes requires complex and time-consuming computations.
Now, researchers from the Harvard John A. Paulson School of Engineering and Applied Sciences (SEAS) have developed a platform that uses machine learning to program the transformation of 2D stretchable surfaces into specific 3D shapes.
“While machine learning methods have been classically employed for image recognition and language processing, they have also recently emerged as powerful tools to solve mechanics problems,” said Katia Bertoldi, the William and Ami Kuan Danoff Professor of Applied Mechanics at SEAS and senior author of the study. “In this work we demonstrate that these tools can be extended to study the mechanics of transformable, inflatable systems.”
The research is published in Advanced Functional Materials.
The research team began by dividing an inflatable membrane into a 10×10 grid of 100 square pixels that can either be soft or stiff. The soft or stiff pixels can be combined in an almost infinite variety of configurations, making manual programming extremely difficult. That’s where machine learning comes in.
The researchers used what’s known as finite element simulations to sample this infinite design space. Then neural networks used that sample to learn how the location of soft and stiff pixels controls the deformation of the membrane when it is pressurized.
“Once the machine learning model was trained, we came up with an arbitrary 3D shape and passed it to the model,” said Antonio Elia Forte, a former postdoctoral fellow at SEAS and first author of the paper. “The neural network then outputs the membrane design and the pressure at which we should inflate such membrane to obtain the desired 3D shape.”
The researchers used this new design method to build and test a device for mechanotherapy that can stimulate tissue around a scar to enhance healing and reduce recovery time.
“This platform has potential to quickly and effectively design patient-specific devices for mechanotherapy and beyond,” said Forte. “Before this research, we didn’t know how to use machine learning to unravel nonlinear mappings in inflatable systems but it turns out that they are very powerful for these purposes.”
The platform can be used to design morphable surfaces at multiple scales for applications from medical devices to architecture.
This is just the beginning of machine-learning enabled design of transformable materials, said Forte.
“Machine learning could push the boundaries of currently known design strategies and allow us to design and build fully reconfigurable shape-morphing material,” said Forte.
The research was co-authored by P. Z. Hanakata, L. Jin, E. Zari, A. Zareei, M. C. Fernandes, L. Sumner and J. Alvarez. The research was supported in part by the National Science Foundation through grants DMR-2011754, DMREF-1922321, OAC-2118201 and DMR-1608501. https://www.seas.harvard.edu/news/2022/01/machine-learning-morphable-materials
Recent Comments